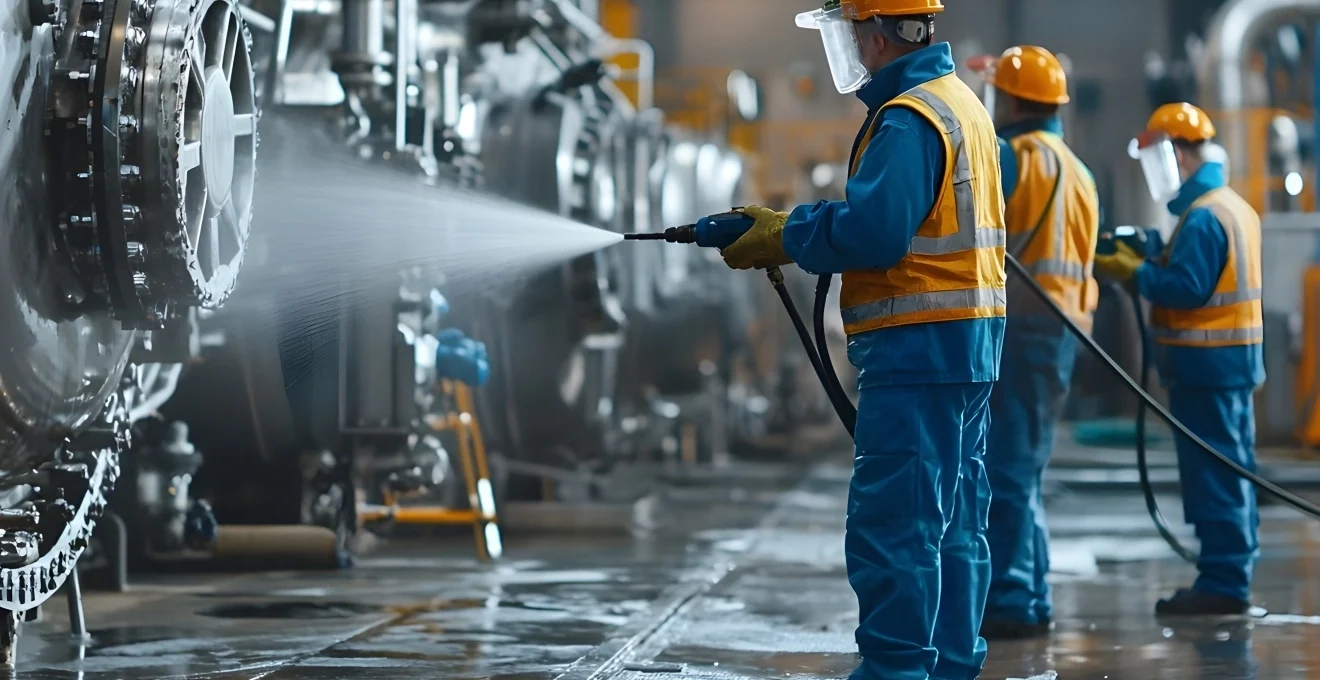
Industrial cleaning plays a pivotal role in maintaining workplace safety and hygiene, particularly in sectors where contamination risks are high. As manufacturing processes become more complex and regulatory standards more stringent, the importance of effective cleaning strategies cannot be overstated. Modern industrial cleaning techniques not only ensure a visually clean environment but also contribute significantly to employee health, product quality, and overall operational efficiency.
The evolution of industrial cleaning technologies has revolutionized how businesses approach workplace contamination control. From advanced filtration systems to innovative disinfection methods, these technologies are designed to tackle a wide range of contaminants, from microscopic particles to harmful microorganisms. But how exactly do these cutting-edge solutions enhance safety and hygiene in industrial settings?
Industrial cleaning technologies for workplace contamination control
The landscape of industrial cleaning has been transformed by technological advancements aimed at improving contamination control. These innovations address various aspects of cleanliness, from air quality to surface decontamination. One of the most significant developments in this field is the integration of data-driven approaches, allowing for more precise and efficient cleaning protocols.
Advanced cleaning technologies now incorporate sensors and IoT devices to monitor contamination levels in real-time. This data-driven approach enables facilities to implement targeted cleaning strategies, focusing resources on areas that require immediate attention. By leveraging analytics, industrial cleaning becomes more proactive rather than reactive, significantly reducing the risk of contamination-related incidents.
HEPA filtration systems for airborne particulate removal
High-Efficiency Particulate Air (HEPA) filtration systems stand at the forefront of air quality control in industrial environments. These systems are designed to capture particles as small as 0.3 microns with an efficiency of 99.97%. In industries where airborne contaminants pose significant health risks, HEPA filters are invaluable for maintaining a safe working atmosphere.
The implementation of HEPA filtration goes beyond simply improving air quality. It also contributes to the longevity of sensitive equipment by reducing the accumulation of dust and other particulates. This dual benefit of protecting both personnel and machinery underscores the importance of comprehensive air filtration strategies in industrial cleaning protocols.
Chemical exposure limits and PPE requirements in cleaning operations
Industrial cleaning often involves the use of potent chemicals, necessitating strict adherence to exposure limits and proper use of Personal Protective Equipment (PPE). The Occupational Safety and Health Administration (OSHA) sets Permissible Exposure Limits (PELs) for various chemicals used in cleaning operations. Compliance with these limits is crucial for preventing adverse health effects among cleaning staff and other employees.
PPE requirements for industrial cleaning operations vary depending on the chemicals and processes involved. Typically, this includes gloves, eye protection, respiratory equipment, and protective clothing. The selection of appropriate PPE must be based on a thorough risk assessment of the cleaning tasks and the specific chemicals in use. Regular training on PPE use and maintenance is essential to ensure its effectiveness in protecting workers from chemical exposure.
Ergonomic considerations in industrial cleaning equipment design
The design of industrial cleaning equipment has evolved to incorporate ergonomic principles, reducing the physical strain on cleaning staff and minimizing the risk of repetitive stress injuries. Ergonomically designed equipment not only improves worker comfort but also enhances efficiency and thoroughness in cleaning operations.
Key ergonomic features in modern cleaning equipment include adjustable handles, lightweight materials, and improved maneuverability. These design elements allow cleaning staff to maintain proper posture and reduce the force required to operate the equipment. By prioritizing ergonomics, industrial facilities can reduce workplace injuries and improve the overall effectiveness of their cleaning programs.
Noise reduction strategies for industrial cleaning machinery
Excessive noise from cleaning machinery can pose significant health risks to workers, including hearing loss and increased stress levels. Implementing noise reduction strategies is crucial for maintaining a safe and comfortable work environment. Modern industrial cleaning equipment often incorporates noise-dampening technologies to minimize sound emissions without compromising cleaning performance.
Strategies for noise reduction in industrial cleaning include:
- Using sound-absorbing materials in equipment construction
- Implementing vibration isolation techniques
- Designing enclosed cleaning systems to contain noise
- Scheduling noisy cleaning operations during off-peak hours
By addressing noise concerns, industrial facilities can create a more pleasant working environment and reduce the long-term health impacts associated with prolonged exposure to loud machinery.
OSHA standards and industrial hygiene compliance in cleaning protocols
Compliance with OSHA standards is paramount in industrial cleaning operations. These standards encompass a wide range of safety and health requirements, including hazard communication, respiratory protection, and exposure limits for various chemicals. Industrial hygiene compliance ensures that cleaning protocols not only achieve cleanliness but also prioritize worker safety and health.
Key aspects of OSHA compliance in industrial cleaning include:
- Conducting regular risk assessments of cleaning operations
- Implementing comprehensive hazard communication programs
- Providing adequate training on safe cleaning practices and chemical handling
- Maintaining proper documentation of safety procedures and incidents
Adhering to these standards not only protects employees but also shields companies from potential legal liabilities associated with workplace safety violations. Regular audits and updates to cleaning protocols ensure ongoing compliance with evolving OSHA regulations.
Microbial decontamination methods in High-Risk industrial environments
In high-risk industrial environments, such as pharmaceutical manufacturing or food processing facilities, microbial contamination can have severe consequences. Advanced decontamination methods are essential for maintaining the sterility required in these settings. These methods go beyond traditional cleaning techniques, targeting microscopic organisms that can compromise product safety and quality.
UV-C light disinfection for surface sterilization
Ultraviolet-C (UV-C) light disinfection has emerged as a powerful tool for surface sterilization in industrial environments. This method uses short-wavelength ultraviolet light to destroy the DNA of microorganisms, rendering them unable to reproduce. UV-C disinfection is particularly effective in areas that are difficult to clean using traditional methods, such as HVAC systems or intricate machinery components.
The advantages of UV-C disinfection include:
- Chemical-free sterilization, reducing environmental impact
- Rapid treatment times, allowing for frequent disinfection cycles
- Effectiveness against a wide range of pathogens, including antibiotic-resistant bacteria
- Minimal disruption to operations, as areas can be quickly returned to use after treatment
Electrostatic spraying techniques for uniform chemical application
Electrostatic spraying has revolutionized the application of disinfectants and sanitizers in industrial settings. This technique uses an electrical charge to attract cleaning solutions to surfaces, ensuring uniform coverage and reducing waste. The result is a more efficient and thorough disinfection process, particularly on complex or hard-to-reach surfaces.
Electrostatic spraying offers several benefits for industrial cleaning:
"Electrostatic technology allows for 360-degree coverage of surfaces, ensuring that even hidden areas receive proper disinfection. This level of thoroughness is crucial in high-risk environments where complete sanitization is non-negotiable."
Hydrogen peroxide vapor decontamination for sensitive equipment
Hydrogen peroxide vapor (HPV) decontamination is a highly effective method for sterilizing sensitive equipment and enclosed spaces. This process involves the vaporization of hydrogen peroxide, which penetrates all areas of a room or enclosure, effectively eliminating a wide range of microorganisms. HPV is particularly valuable in cleanrooms, isolators, and other controlled environments where traditional cleaning methods may be insufficient or impractical.
The HPV decontamination process typically involves the following steps:
- Sealing the area to be decontaminated
- Injecting vaporized hydrogen peroxide into the space
- Maintaining the vapor concentration for a specified contact time
- Aerating the area to remove residual vapor
- Verifying successful decontamination through biological indicators
Biofilm removal strategies in food processing facilities
Biofilms pose a significant challenge in food processing environments, as they can harbor pathogenic bacteria and resist traditional cleaning methods. Effective biofilm removal requires a combination of mechanical action, chemical treatment, and specialized cleaning protocols. Advanced strategies for biofilm removal include enzymatic cleaners, which break down the extracellular matrix of biofilms, and high-pressure cleaning systems that dislodge stubborn bacterial colonies.
Implementing a comprehensive biofilm prevention and removal program involves:
- Regular surface inspections to identify potential biofilm formation sites
- Use of materials and surface finishes that resist biofilm attachment
- Implementation of cleaning rotation schedules to prevent bacterial adaptation
- Application of specialized biofilm-disrupting agents as part of routine cleaning
Hazardous material handling and disposal in industrial cleaning
The handling and disposal of hazardous materials are critical components of industrial cleaning operations. Proper management of these substances is essential for protecting worker safety, complying with environmental regulations, and preventing contamination of products or the environment. Facilities must develop comprehensive protocols for identifying, handling, storing, and disposing of hazardous cleaning agents and waste.
Key considerations in hazardous material management include:
- Proper labeling and storage of hazardous cleaning agents
- Training staff on safe handling procedures and emergency response
- Implementing spill containment and cleanup protocols
- Ensuring proper disposal through licensed waste management services
Facilities should also explore opportunities to reduce the use of hazardous materials through the adoption of green cleaning technologies and practices. This approach not only enhances safety but also aligns with broader sustainability goals.
Data-driven cleaning management: IoT and analytics in workplace hygiene
The integration of Internet of Things (IoT) devices and data analytics is transforming industrial cleaning management. These technologies enable real-time monitoring of cleanliness levels, equipment performance, and resource utilization. By leveraging data-driven insights, facilities can optimize cleaning schedules, allocate resources more efficiently, and identify trends that inform long-term hygiene strategies.
IoT applications in industrial cleaning include:
- Smart dispensers that monitor cleaning agent usage and trigger refills
- Sensors that detect contamination levels and alert staff to cleaning needs
- Wearable devices that track cleaning staff movements and task completion
- Connected cleaning equipment that reports performance data and maintenance requirements
Analytics platforms aggregate data from these IoT devices, providing facility managers with comprehensive dashboards and reports. This information enables data-driven decision-making, leading to more effective and efficient cleaning operations.
Cross-contamination prevention strategies in Multi-Zone industrial facilities
In multi-zone industrial facilities, preventing cross-contamination between areas with different cleanliness requirements is crucial. This is particularly important in industries such as pharmaceuticals, electronics manufacturing, and food processing, where contamination can have severe consequences for product quality and safety.
Effective cross-contamination prevention strategies include:
- Implementing color-coded cleaning equipment for different zones
- Establishing clear protocols for personnel and equipment movement between zones
- Using airlocks and differential pressure systems to maintain clean zone integrity
- Regular validation of cleaning effectiveness through environmental monitoring
By implementing robust cross-contamination prevention measures, facilities can maintain the integrity of clean zones and ensure consistent product quality across all areas of operation.
The landscape of industrial cleaning continues to evolve, driven by technological advancements and a growing emphasis on workplace safety and hygiene. From sophisticated air filtration systems to data-driven cleaning management, these innovations are reshaping how industries approach contamination control. As regulations become more stringent and the importance of workplace health gains greater recognition, investing in advanced cleaning technologies and protocols is no longer optional but essential for operational excellence and employee well-being.